top of page

INVISIBLE
FORCE
보이지 않는 힘
Signe-S를 통해 Hyper-Automation을 실현할 수 있습니다.
AI 기반 스마트팩토리는 AI를 활용한 엔지니어링 보고서 등 휴먼 프로세스를 넘어서서 모든 공정이 AI에 의해 감시 원인도출 예측 제어 유지 관리되는 실시간 자동화 체제입니다. Signe-S는 AI에 의해 실시간 엔지니어링을 실현할 수 있는 솔루션입니다.
Signe-S Ecosystem은 고객사의 OEE 극대화를 위한
Hyper-Automation 지향 솔루션이며 Cross Platform을 지원합니다.
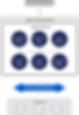
자율형 설비 공정 이상 감시 시스템
AI-based Fault Detection and
Classification
설비 및 공정 조건 변동 자율 감시
(No Spec setting)
자율형 가상계측 시스템
AI-based Virtual Metrology
공정 변화와 같은 동적인 대상에 대해 정확한 예측이 필요할 때 사용 (No Retraining)
지능형 공정 진단 시스템
AI-based Machine Learning
인공지능 지원 Machine Learning
쉽고 빠르고 정확한 공정 진단 및
기계학습
자율형 공정제어 시스템
AI-based Advanced Process Control
연결만 하면 Target에 접근하게 하고 산포가 감소하도록 최적 공정 조건 자동 설정 (No DOE No Coding)
고용량 고성능 데이터 수집 전송 시스템
Solace Event Platform for Event Mesh
공장 내 모든 고용량 정형, 비정형 데이터 및 이벤트, 로그, 이미지 파일 등 실시간 수집 가공 및 전송

Industry 4.0 Smart Factory AI Solution

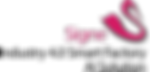
Signe-S Architecture for Industry 4.0

Signe-S AI Solution에 대한 자세한 내용은
DSEY 대표번호 및 담당자에게 문의하시기 바랍니다.
bottom of page